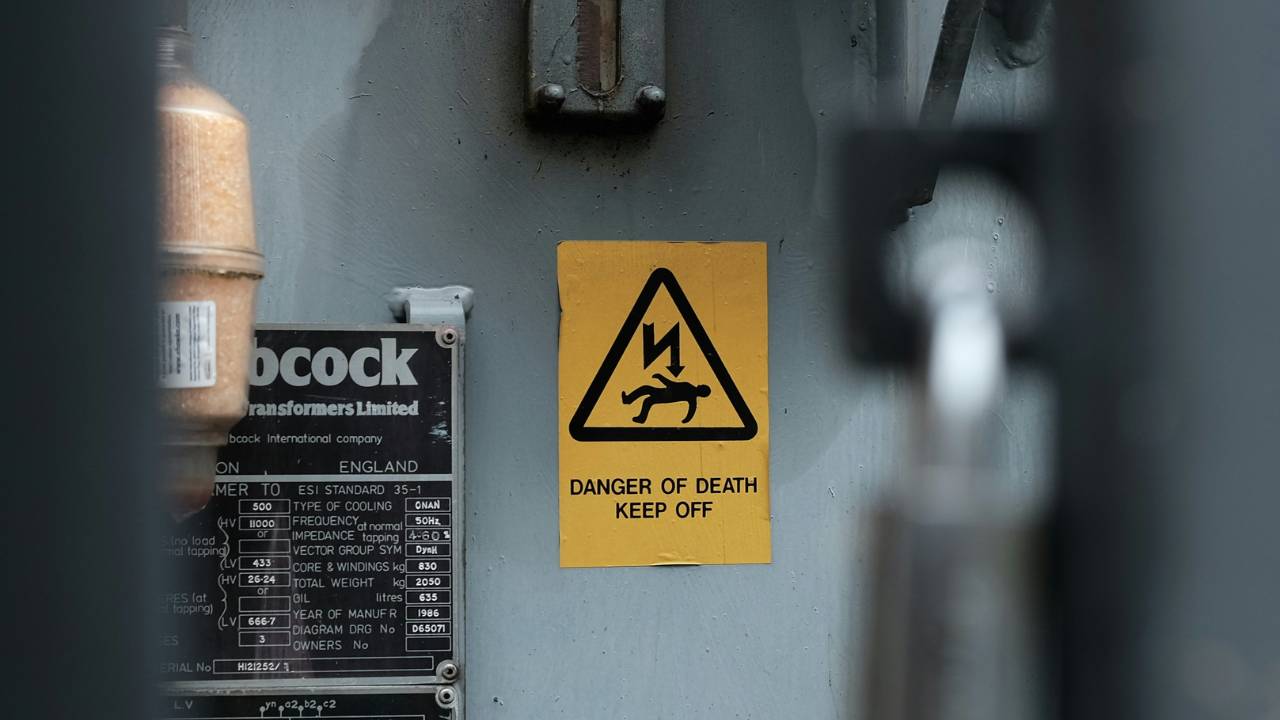
Electrical safety isn’t just a regulatory checkbox – it’s a fundamental business responsibility with far-reaching implications. For small businesses across Ireland, navigating the complex landscape of electrical compliance can be particularly challenging. Limited resources, multiple regulatory requirements, and the day-to-day pressures of running a business often push electrical safety protocols into the background.
Understanding the law on PAT testing is just one piece of the puzzle when it comes to ensuring complete electrical safety in the workplace. From Dublin to Cork, Galway to Limerick, countless small enterprises inadvertently put themselves, their employees, and their customers at risk through non-compliance – not through negligence, but through simple misunderstanding or oversight.
Mistake #1: Skipping Portable Appliance Testing (PAT) or Doing It Infrequently
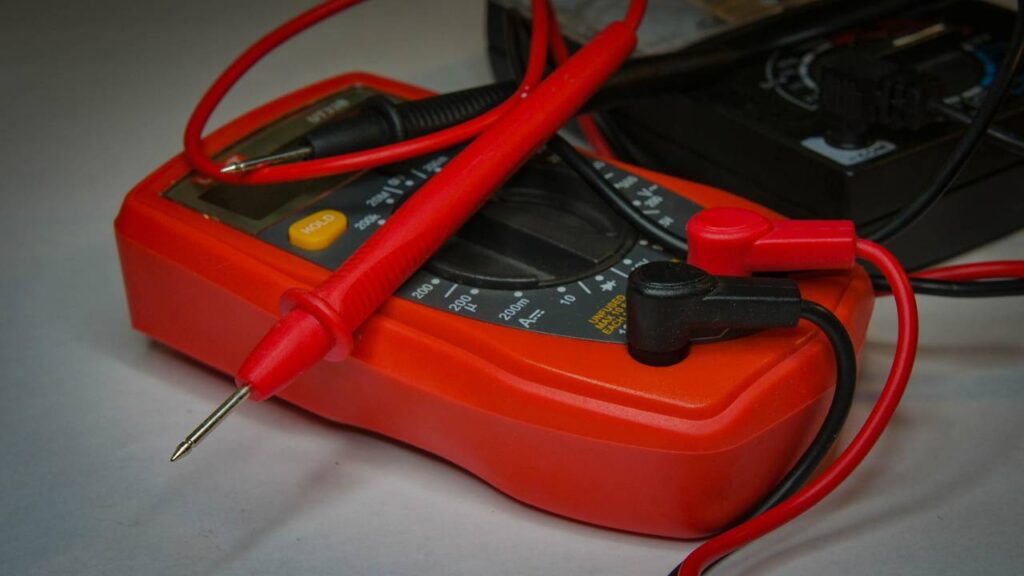
Portable Appliance Testing (PAT) is one of the most recognisable electrical safety requirements, yet it remains frequently misunderstood and inconsistently implemented across small businesses in Ireland.
PAT testing involves inspecting and testing portable electrical appliances – essentially anything with a plug – to ensure they’re safe for continued use. This includes computers, printers, kettles, power tools, extension leads, and countless other devices found in workplaces.
While many business owners believe PAT testing is legally required annually for all appliances, the reality is more nuanced. Electrical safety compliance for Irish businesses starts with understanding what appliances need to be tested and how often. The appropriate testing frequency depends on several factors:
- The type of equipment (Class I or Class II)
- The environment in which it’s used
- The level of user handling
- The manufacturer’s recommendations
- Previous test results and equipment history
For example, a desktop computer in an office environment typically needs less frequent testing than a power drill used on construction sites. The Safety, Health and Welfare at Work (General Application) Regulations 2007 require employers to ensure that electrical equipment is maintained in a safe condition, but they don’t explicitly mandate annual PAT testing for all items.
This doesn’t mean testing can be neglected. Rather, businesses should establish a risk-based testing schedule, documenting their approach and justification. Many insurance policies now specifically require evidence of electrical testing, making compliance not just a legal consideration but a financial one, too.
Common mistakes in this area include:
- Testing everything annually regardless of risk (wasting resources)
- Testing nothing at all (creating liability)
- Testing without proper documentation (leaving no evidence of compliance)
- Using unqualified personnel to conduct tests (invalidating results)
To improve compliance, consider developing a categorised inventory of all portable appliances, with appropriate testing schedules based on risk assessment rather than arbitrary timeframes.
Mistake #2: Using Unqualified Personnel for Electrical Work
In an effort to save costs, many small Irish businesses make the dangerous mistake of using unqualified personnel for electrical installations, repairs, or modifications. This practice not only creates immediate safety risks but potentially invalidates insurance coverage and violates regulations.
In Ireland, electrical work should be carried out by Registered Electrical Contractors (RECs) who are registered with Safe Electric, the statutory regulatory scheme operated by the Register of Electrical Contractors of Ireland (RECI) or the Electrical Contractors Safety & Standards Association (ECSSA).
Using qualified professionals ensures:
- Work meets required standards under the National Rules for Electrical Installations (ET101)
- Appropriate certification is provided upon completion
- Insurance coverage remains valid
- Business owners fulfil their duty of care
The temptation to have a “handy” staff member handle minor electrical work is particularly common in retail, hospitality, and small manufacturing operations. However, even seemingly simple tasks like replacing light fixtures or installing additional sockets require proper qualification.
The consequences of improper electrical work can be catastrophic. Beyond immediate safety risks, businesses may face prosecution under the Safety, Health and Welfare at Work Act 2005 if an incident occurs involving non-compliant electrical installations.
When hiring electrical contractors, always:
- Verify their Safe Electric registration
- Request references from previous commercial clients
- Ensure they provide appropriate certification upon completion
- Keep records of all work completed, including dates and scope
Even for temporary electrical installations – such as for events or seasonal decorations – qualified personnel are essential. The brief nature of the installation doesn’t diminish the safety requirements or potential liability.
Mistake #3: Not Keeping Records of Electrical Inspections and Repairs
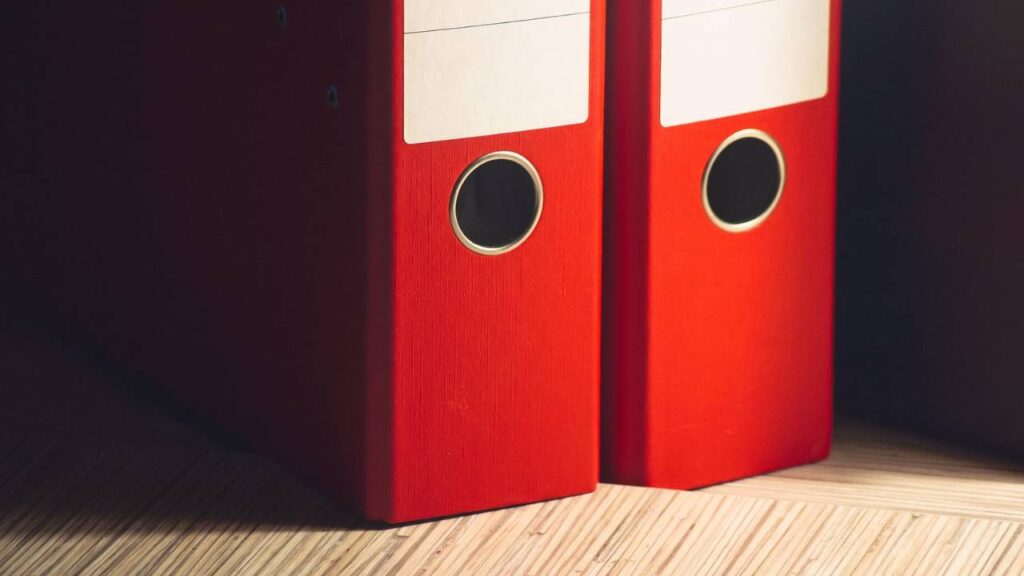
Poor record-keeping is a pervasive issue among small businesses across all sectors. When it comes to electrical compliance, documentation isn’t just good practice – it’s often the only evidence you have to demonstrate due diligence.
Many Irish business owners diligently arrange inspections and promptly address issues yet fail to maintain proper records of this work. In the eyes of regulators, insurers, and the courts, compliance without documentation is effectively non-compliance.
Essential electrical safety records include:
- PAT testing certificates and results
- Installation certificates for new electrical work
- Periodic inspection reports
- Maintenance and repair logs
- Risk assessments
- Staff training records related to electrical safety
These records serve multiple critical functions:
- Demonstrating regulatory compliance to HSA inspectors
- Supporting insurance claims in case of electrical incidents
- Providing evidence of due diligence in legal proceedings
- Tracking equipment lifecycle and planning for replacements
- Identifying recurring issues that may indicate systemic problems
Digital record-keeping systems have made compliance documentation more accessible for small businesses. Cloud-based solutions allow for easy storage, retrieval, and sharing of certificates and reports when needed. However, even a well-organized paper filing system is far better than no system at all.
For businesses operating across multiple sites, centralised record-keeping becomes even more critical. Each location should maintain its own documentation, with copies available centrally for management oversight and compliance monitoring.
Mistake #4: Ignoring the Need for Regular Fixed Wire Testing
While many businesses focus on portable appliance testing, fixed electrical installations often receive less attention despite posing equal or greater risks. This includes fixed appliance testing, which assesses the safety of equipment permanently connected to the electrical supply, such as built-in kitchen devices or HVAC units. Fixed wire testing, also known as Electrical Installation Condition Reporting (EICR) or Periodic Inspection and Testing, evaluates the safety of your building’s permanent electrical systems.
This includes:
- Consumer units and distribution boards
- Wiring systems
- Earthing and bonding
- Fixed machinery connections
- Lighting systems
- Socket outlets and switches
Unlike PAT testing, which can sometimes be conducted by trained in-house personnel, periodic inspection and testing of fixed installations must be carried out by qualified electricians. The recommended frequency varies based on the property type and use:
- Commercial premises: Every 5 years
- Industrial premises: Every 3 years
- Restaurants and hotels: Every 5 years
- Construction sites: Every 3 months
- Properties with swimming pools: Annually
- Rental properties: Every 5 years or change of tenancy
Many business owners mistakenly believe that once electrical installations are complete, they require no further attention until problems arise. This approach ignores how electrical systems deteriorate over time due to wear, environmental factors, and modifications.
Signs that fixed wire testing is overdue include:
- Frequent circuit breaker trips
- Flickering lights
- Warm or discoloured sockets or switches
- Burning smells with no obvious source
- Ageing distribution boards (particularly those over 25 years old)
For businesses operating in leased premises, there’s often confusion about responsibility for fixed electrical installations. While specific arrangements vary by lease agreement, generally, the tenant is responsible for maintaining electrical installations within their occupied space, while the landlord is responsible for common areas and incoming supplies.
Mistake #5: Delaying Repairs or Temporary Fixes Becoming Permanent
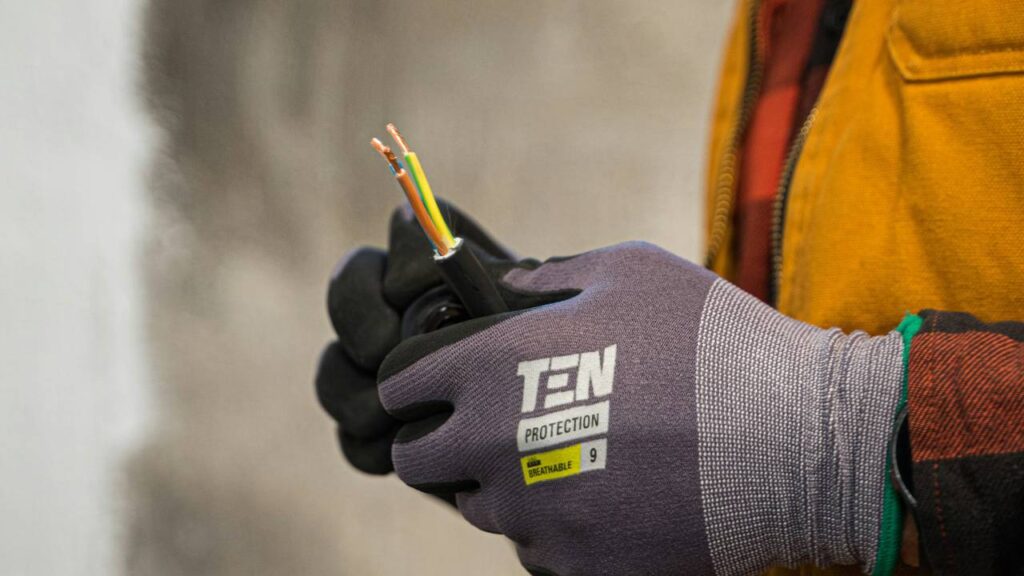
In busy commercial environments, temporary electrical solutions often become permanent by default. Extension leads run as permanent wiring, damaged equipment remains in service with makeshift repairs, and “do not use” tags stay in place for months while proper repairs are postponed.
These temporary fixes create significant hazards and represent one of the most common factors in workplace electrical incidents. The HSA repeatedly identifies this issue during inspections, particularly in retail, hospitality, and small manufacturing operations.
Neglecting electrical safety in your company can cost you a lot – not just in potential fines but in avoidable downtime, insurance issues, and even legal liability. When electrical issues are identified, they should be categorised by severity and addressed accordingly:
- Code 1 (Danger present): Requires immediate action
- Code 2 (Potentially dangerous): Requires urgent attention
- Code 3 (Improvement recommended): Should be scheduled for repair
- Code 4 (Further investigation required): Needs additional assessment
Common examples of dangerous temporary fixes include:
- Daisy-chained extension leads
- Overloaded sockets or adaptors
- Tape-wrapped damaged cables
- Inappropriate use of equipment (indoor equipment used outdoors)
- Removed covers or protective housings
- Bypassed safety devices
Establishing clear procedures for reporting electrical issues and scheduling repairs is essential. All staff should understand the importance of prompt reporting, and management should allocate resources for timely resolution rather than temporary workarounds.
For seasonal businesses, the off-season provides an ideal opportunity to address electrical maintenance comprehensively rather than implementing quick fixes during busy periods that inevitably become permanent.
Conclusion
Electrical compliance doesn’t have to be overwhelming. By avoiding these five common mistakes – such as skipping PAT testing, using unqualified personnel, or failing to keep proper records – small Irish businesses can stay on the right side of safety laws and reduce their risk exposure.
Ultimately, electrical safety compliance for Irish businesses is about more than just regulations – it’s about safeguarding your people, property, and reputation. Taking a proactive approach today can save your company from serious consequences tomorrow.